Translation in progress...Anfertigen und Verlegen des HolzdecksIch habe mein ursprüngliches Layout leicht modifiziert und vereinfacht. Die Mahagoni-Leibhölzer habe ich aus einem 1-Zoll-Brett vorbereitet. Durch Halbieren der einzelnen Teile entstehen spiegelbildliche Masserungsmuster. Nach dem Hobeln blieb eine nutzbare Stärke von 11 mm.
Die Leibhölzer am Süllrand mitschiffs und hinten mussten wegen der Deckskrümmung mit Dampf vorgebogen werden. Die Spannung wäre sonst zu hoch gewesen. Zur Problematik des Dampfbiegens siehe weiter unten.
Ausgehend von diesen drei gebogeben Teilen habe ich die restlichen Leibhölzer nach und nach angepasst und mit 4,8 mm Blechschrauben provisorisch befestigt.

Mahagoni-Leibhölzer des Achterdecks...
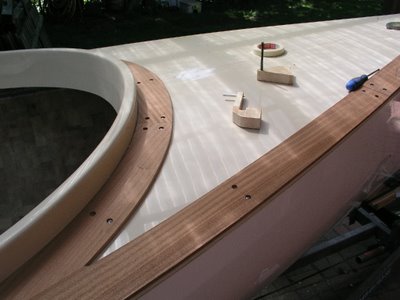
... und die des Vorderdecks
Danach wurden die Teile abgenommen und mit verdünntem Klarlack grundiert.
Vor dem Kleben mit Sikaflex müssen die entsprechenden Bereiche des Decks angeschliffen werden (Gelcoat adé, muss aber sein...). Desgleichen musste ich die Tankfüllverschraubung auf dem Vorderdeck abbauen, was durch Nachlässigkeit der Werft keine leichte Aufgabe war (die Verschraubung ist mit dem Gelcoat fest verklebt; es wurde offensichtlich kein Trennmittel eingesetzt).Kleben mit Sikaflex allein geht nicht, die Befestigung mit den kräftigen Blechschrauben ist unerläßlich.Wie geplant, habe ich die Decksleisten aus Teakbohlen gesägt, gehobelt und gefräst. Ich entschied mich für eine Nutenbreite von 5 mm. Die Leisten zeigen z.T. ausgeprägte Verfärbungen, die laut Aussage des Holzhändlers nach Sonneneinstrahlung nach und nach verschwinden.
Die Leisten zu verlegen hat ordentlich Spaß gemacht. Zuerst wurden sie grob angepasst und verschraubt, dann zu den Leibhölzern hin markiert, wieder abgenommen und genau auf Kontur gebracht.
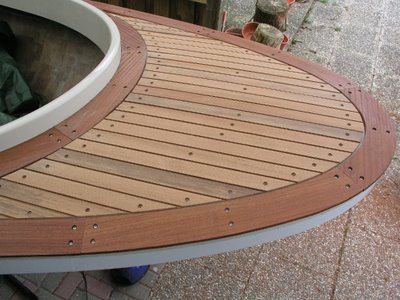
So sehen jetzt das Achterdeck...

... und das Vorderdeck aus
Die Leisten müssen nun wieder abgenommen und mit Sikaflex endgültig verlegt werden. Die Reihenfolge der nächsten Schritte (Pfropfen einkleben, verschleifen, verfugen mit Sikaflex 290 DC, usw.) habe ich mit einem Kollegen besprochen, der so etwas bereits gemacht hat (schönen Dank, Migges).
Nächste Woche geht's weiter. Anschließend kommt die Scheuerleiste dran. Die 4 Längen (4,5 m, Querschnitt 40 x 20 mm) habe ich bereits aus einer sehr breiten Mahagoni-Bohle gesägt und gehobelt.
Translation in progressHolzbiegen mit einfachen MittelnFür einige Arbeiten im Bootsbau ist es unerläßlich, Holzteile mit Dampf zu biegen. Man braucht jedoch dazu keine Werftsmäßige Ausrüstung, es geht auch mit einfachen, selbsgebastelten Mitteln.
Beim Ausbau des Rumpfes habe ich das Verfahren bereits zweimal anwenden müssen: bei den Decksleibhölzern (siehe oben) und beim hinteren Teil der Scheuerleiste.
Wegen der leichten Krümmung bereiten die Leibhölzer keine Schwierigkeiten. Man braucht dazu eine Dampfkiste und eine Biegeform.Meine Dampfkiste besteht aus zusammengeschraubten Sperrholzbrettern, mittig sitzend auf dem "Dampfgenerator" (ein Ikea-Edelstahltopf mit 4, im Topfboden eingesetzten Siedeschlangen aus ausgeschlachteten, billigen Wasserkochern. Das Ganze wird mit 380 V betrieben).

Die Dampfkiste, die schon dutzende von Leisten weich gekocht hat
Die Biegeform habe ich aus einem Stück Restholz gesägt. Da das Holz nach dem Entformen nachfedert, muss die Krümmung der Form etwas stärker als die des Decks sein.

Die Biegeform aus einem Stück Restholz

... und mit eingeklemmten Leibholz nach dem Dämpfen
Eine andere Geschichte ist das Biegen des hinteren Teils der Scheuerleiste. Die Querschnittabmessungen und die starke Krümmung erfordern "besondere" Massnahmen.
Die Kontur der Biegeform wird direkt vom Deck abgenommen, und ebenfalls etwas enger gezeichnet. Da beim Biegen beträchtliche Kräfte entstehen, sollte die Form stabil gestaltet werden. Erneut habe ich dazu Restholz genommen (alte Zaunpfosten).
Jetzt zu den besonderen Maßnahmen. Einfach über die Form Biegen, nachdem das Holz die entsprechnde Zeit in der Dampfkiste war, führt unweigerlich zum Bruch.
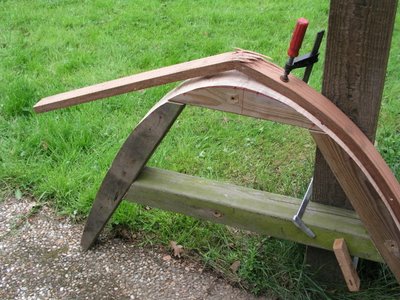
Biegeversuch "ohne Sinn und Verstand"...
Wenn man weißt, worum es dabei geht, kann man jedoch dickere Leisten problemlos um enge Radien biegen. Folgendes (eigene Erfahrung) soll berücksichtigt werden:
1. Kammergetrocknetes Holz (praktisch das Einzige, was man bekommen kann) eignet sich nicht zum Biegen. Die Holzfasern sind einfach zu trocken; dämpfen reicht nicht aus, um sie zu erweichen. Ich wässere die Rohlinge ca. drei Tage lang im Teich, bis das Holz durchgehend feucht ist.
2. Nach dem "Weichkochen" in der Dampfkiste lassen sich die Holzfasern durch Druck klaglos ineinander schieben (verkürzen). Dagegen lassen sie sich schlecht auseinander ziehen, bereits eine leichte Dehnung führt zum Bruch. Das ist der Fall bei dickeren Leisten oder engeren Radien.3. Die Oberfläche des Rohlings und die Biegefläche der Form müssen glatt sein. Dadurch wird das Ineinanderschieben der Fasern an der innenseite der Biegung nicht "gebremst". Die Biegefläche der Form belege ich daher mit einem Streifen aus Niroblech.
4. Es muss verhindert werden, dass die Fasern an der Außenseite der Biegung länger werden. Dies wird dadurch erreicht, dass der Rohling zwischen zwei Holzklötzen eingeklemmt wird, die an einem Stahlband (Kompressionsband) festgeschraubt sind. Den genauen Abstand dieser Anschlagklötze muss im nassen Zustand des Rohlings eingestellt werden. Seine Länge ändert sich nicht mehr nach dem Dämpfen. Beim Biegen können sich die äußeren Schichten nicht verlängern, nur die Innenseite wird dann kürzer.
5. Da es beim Biegen alles schnell gehen muss, ist es vorteilhaft, wenn man vorher die Bewegungsabläufe eingeübt hat.
6. Das Hantieren mit Schraubzwingen nimmt viel Zeit in Anspruch. Durchgesteckte Bolzen und Keile sind schneller und sicherer.
7. Das Holz erst in die Kiste legen, wenn die angezeigte Temperatur ca. 95 °C überschritten hat. Ab dann, keine Unterbrechung, sonnst muss man wieder von vorn anfangen.
8. Nach der Dämpfzeit (ca. 1 Stunden pro Zoll) wird der Rohling eingeklemmt und zügig um die Form gebogen. Streckenweise werden die Haltebolzen durchgesteckt und mit Keilen gesichert.

Vorbereitete Biegeform. Auf der Innenfläche, das "Rutschband". Auf der rechten Seite, das Kompressionsband, einseitig befestigt und bereits auf die Länge der Leiste eingestellt

Die 1-Zoll-Mahagonileiste nach dem Biegen. Außen, das Kompressionsband mit den Anschlagklötzen (Reststücke Mahagonileiste)
Nach ein paar Stunden können die Metallbänder entfernt werden. Die Leiste muss jedoch fest geklemmt auf der Form bleiben, damit sie vollständig trocknen kann (ca. 1 Woche).
Beginning of the Year to the Present Day
Description of the Boat
So called "Fantail Launch"
Length over all: 23' 3" (7,028 m)
Breadth over all: 6' 3" (1,900 m)
Draft: 1" 6.25" (0,46 m) @ 2906 lbs (1.3 tons)The boat was designed in 1982 by Pat Spurlock (Elliott Bay Co. in Portland, Oregon). It is based on the lines of 5 Victorian Era (1870-1900) hulls, all of them with an approximate length of 23 feet. This fantail launch has been described in detail in the specialized literature. Made of cored (balsa wood) glass polyesther composite. The deck (also a sandwich construction) is already bonded to the hull. The hull is supplied with engine bearers, bow tank, floor timber, stern tube and tiller port structures already in place.
Picking-up TripThe Elliott Bay Co., from which I ordered the boat at the beginning of February, has a selling agent in Holland (the ELOship Co. in Groningen). They had two hulls in stock and readily available. The weather however was not part of the game, testing my ability to wait patiently during a couple of weeks (I had a bad time...)
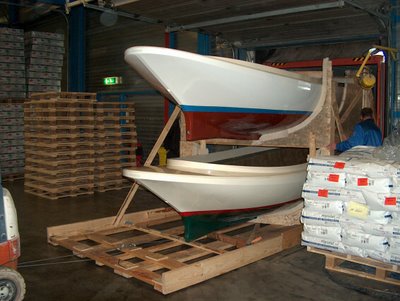
The boats are being pulled from the container
During the waiting time I ordered the equipment parts available in Groningen: 20" x 30" wheel, sterntube with shaft bearing , rudder with tiller and bearing, and the skeg.
After the weather seemed to become a bit more friendly, I arranged a picking-up date with Mr. Bäcker of ELOship for the 10th of March. And just on this day a heavy, unspected snow storm swept over the Northern part of Germany. I spent 3 hours to drive past the Hamburg area, which usually takes some 30 minutes. During the return trip I encountered icy rain conditions, so that I had to stay overnight somewhere near to Emden.
Next morning in Remels, where I stayed overnight
Weather conditions had suddenly changed overnight, driving back home was a pleasurable trip. However, the boat had to wait a couple of weeks under a plastic cover at the backyard, the weather still being unusually cold. It was not before the beginning of April that I could pull the trailer over the lawn to reach the "First and Only Steam Boat Yard of Böhnhusen", a roofed pergola attached to our house.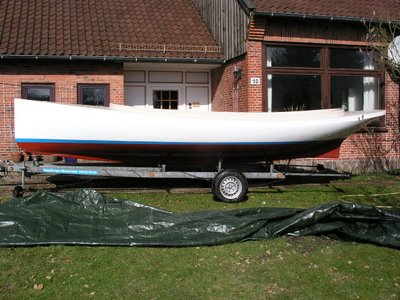
Underway on the garden, looking for the boat yard...
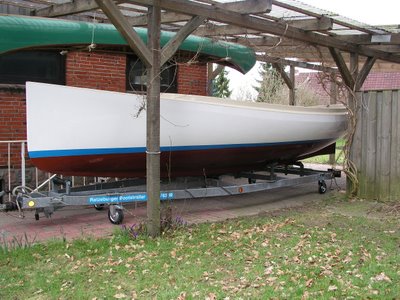
The new home for the next couple of months
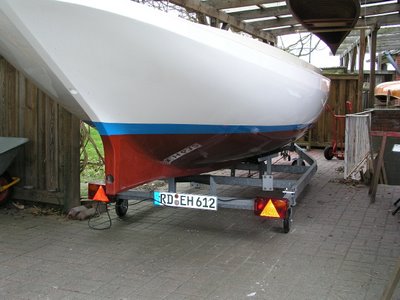
A bit narrow, but the workshop is just downstairs in the basement
The boat remains sitting on the trailer during the entire finishing time. In order to allow for an easier access to the boat, and to be able to move the trailer sideways, I have removed the trailer shaft and mounted four rollers under the frame.
General Considerations
I am certainly not a fan of "plastic bathtubes", I love the traditional wooden boats. For this project however, an important argument was decisive: steam boats are often trailed over hundreds of miles, being thereby subject to an extraordinary strain because of the considerable weight of boiler and steam engine. A traditional wooden boat – irrespective of its type of construction – does not withstand such peak loads for a long time. Its structure softens and gets more and more weak with every trip. Not affected are such types of construction like cold molded and glass-covered wooden strip. I find very remarkable that the French colleagues have a preference for traditional, lapstrake boats with wineglass-type transom.
A further reason for selecting a composite hull is the considerably reduced finishing time. The Elliott Bay hull can even be used without much finishing work.

The additional equipment

Looking forward: engine bearers and floor timber

Looking backwards: Rudder bearing and sterntube support
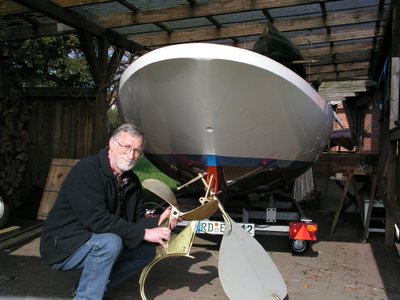
and of course the beautiful screw (wheel)...
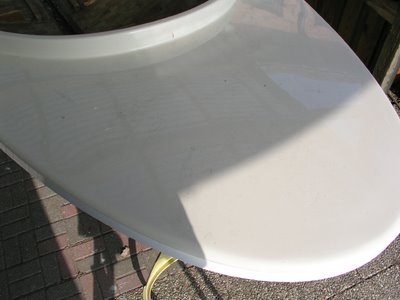
After deck

Fore deck
Planned Activities
All visible plastic surfaces should be covered with a wooden layer, in a similar way as carried out on the other Elliott Bay hulls of the German Steam Boat Association. It would be quite reasonable to start with the floor structure and panels. But I am not that reasonable, and would like to start with the lay-on wooden deck... ..
I am going to use mahogany for the edging planks of the deck and for the guards, as I still have some boards initially intended for canoe building. I intend to prepare myself the 50-mm-wide deck strips by resawing and planing 2" by 4" teak boards as required. I have the address of a lumber yard which sells quality Burma teak at a reasonable price (about 4000 EUR per cubic meter). Purchasing ready made deck strips is exorbitantly expensive (about 25,000 EUR per cubic meter!!).
I became valuable suggestions from different colleagues, especially concerning the type of adhesive (Sikaflex) and screws to be used for this job. Thanks to Migges (DB "Lagavulin") and to Helmut Strothjohann (DB "Vaporosa").
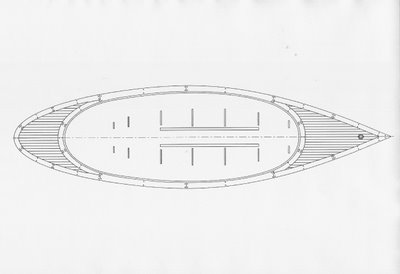
Deck layout
This is how the lay-on deck should look like. Kind of a puzzle work, but I think it looks good, and I'll certainly enjoy doing it. Due to the decks curvature, the edging planks close to the coaming and at the stern must be steam bent.
My shop in the basement is fairly well equipped for this kind of work, including powerful Elektra Beckum Machines (band saw, planing machine, milling machine with feeding unit) as well as an electrical (6 kW) steam box which I have used for canoe building work.
Well, that's all for now. I'll start updating the blogs once a month to report on the progress of my project.