Translation in progress...Anfertigen und Verlegen des HolzdecksIch habe mein ursprüngliches Layout leicht modifiziert und vereinfacht. Die Mahagoni-Leibhölzer habe ich aus einem 1-Zoll-Brett vorbereitet. Durch Halbieren der einzelnen Teile entstehen spiegelbildliche Masserungsmuster. Nach dem Hobeln blieb eine nutzbare Stärke von 11 mm.
Die Leibhölzer am Süllrand mitschiffs und hinten mussten wegen der Deckskrümmung mit Dampf vorgebogen werden. Die Spannung wäre sonst zu hoch gewesen. Zur Problematik des Dampfbiegens siehe weiter unten.
Ausgehend von diesen drei gebogeben Teilen habe ich die restlichen Leibhölzer nach und nach angepasst und mit 4,8 mm Blechschrauben provisorisch befestigt.

Mahagoni-Leibhölzer des Achterdecks...
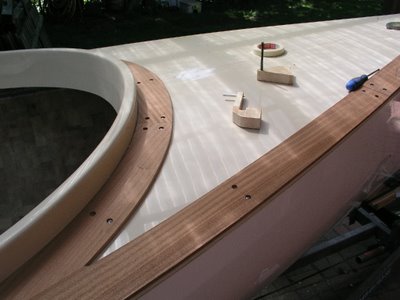
... und die des Vorderdecks
Danach wurden die Teile abgenommen und mit verdünntem Klarlack grundiert.
Vor dem Kleben mit Sikaflex müssen die entsprechenden Bereiche des Decks angeschliffen werden (Gelcoat adé, muss aber sein...). Desgleichen musste ich die Tankfüllverschraubung auf dem Vorderdeck abbauen, was durch Nachlässigkeit der Werft keine leichte Aufgabe war (die Verschraubung ist mit dem Gelcoat fest verklebt; es wurde offensichtlich kein Trennmittel eingesetzt).Kleben mit Sikaflex allein geht nicht, die Befestigung mit den kräftigen Blechschrauben ist unerläßlich.Wie geplant, habe ich die Decksleisten aus Teakbohlen gesägt, gehobelt und gefräst. Ich entschied mich für eine Nutenbreite von 5 mm. Die Leisten zeigen z.T. ausgeprägte Verfärbungen, die laut Aussage des Holzhändlers nach Sonneneinstrahlung nach und nach verschwinden.
Die Leisten zu verlegen hat ordentlich Spaß gemacht. Zuerst wurden sie grob angepasst und verschraubt, dann zu den Leibhölzern hin markiert, wieder abgenommen und genau auf Kontur gebracht.
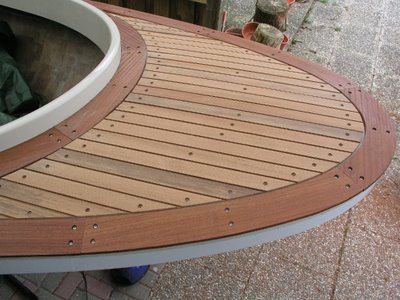
So sehen jetzt das Achterdeck...

... und das Vorderdeck aus
Die Leisten müssen nun wieder abgenommen und mit Sikaflex endgültig verlegt werden. Die Reihenfolge der nächsten Schritte (Pfropfen einkleben, verschleifen, verfugen mit Sikaflex 290 DC, usw.) habe ich mit einem Kollegen besprochen, der so etwas bereits gemacht hat (schönen Dank, Migges).
Nächste Woche geht's weiter. Anschließend kommt die Scheuerleiste dran. Die 4 Längen (4,5 m, Querschnitt 40 x 20 mm) habe ich bereits aus einer sehr breiten Mahagoni-Bohle gesägt und gehobelt.
Translation in progressHolzbiegen mit einfachen MittelnFür einige Arbeiten im Bootsbau ist es unerläßlich, Holzteile mit Dampf zu biegen. Man braucht jedoch dazu keine Werftsmäßige Ausrüstung, es geht auch mit einfachen, selbsgebastelten Mitteln.
Beim Ausbau des Rumpfes habe ich das Verfahren bereits zweimal anwenden müssen: bei den Decksleibhölzern (siehe oben) und beim hinteren Teil der Scheuerleiste.
Wegen der leichten Krümmung bereiten die Leibhölzer keine Schwierigkeiten. Man braucht dazu eine Dampfkiste und eine Biegeform.Meine Dampfkiste besteht aus zusammengeschraubten Sperrholzbrettern, mittig sitzend auf dem "Dampfgenerator" (ein Ikea-Edelstahltopf mit 4, im Topfboden eingesetzten Siedeschlangen aus ausgeschlachteten, billigen Wasserkochern. Das Ganze wird mit 380 V betrieben).

Die Dampfkiste, die schon dutzende von Leisten weich gekocht hat
Die Biegeform habe ich aus einem Stück Restholz gesägt. Da das Holz nach dem Entformen nachfedert, muss die Krümmung der Form etwas stärker als die des Decks sein.

Die Biegeform aus einem Stück Restholz

... und mit eingeklemmten Leibholz nach dem Dämpfen
Eine andere Geschichte ist das Biegen des hinteren Teils der Scheuerleiste. Die Querschnittabmessungen und die starke Krümmung erfordern "besondere" Massnahmen.
Die Kontur der Biegeform wird direkt vom Deck abgenommen, und ebenfalls etwas enger gezeichnet. Da beim Biegen beträchtliche Kräfte entstehen, sollte die Form stabil gestaltet werden. Erneut habe ich dazu Restholz genommen (alte Zaunpfosten).
Jetzt zu den besonderen Maßnahmen. Einfach über die Form Biegen, nachdem das Holz die entsprechnde Zeit in der Dampfkiste war, führt unweigerlich zum Bruch.
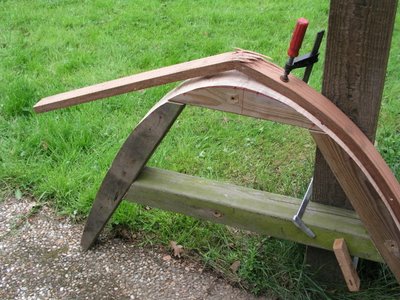
Biegeversuch "ohne Sinn und Verstand"...
Wenn man weißt, worum es dabei geht, kann man jedoch dickere Leisten problemlos um enge Radien biegen. Folgendes (eigene Erfahrung) soll berücksichtigt werden:
1. Kammergetrocknetes Holz (praktisch das Einzige, was man bekommen kann) eignet sich nicht zum Biegen. Die Holzfasern sind einfach zu trocken; dämpfen reicht nicht aus, um sie zu erweichen. Ich wässere die Rohlinge ca. drei Tage lang im Teich, bis das Holz durchgehend feucht ist.
2. Nach dem "Weichkochen" in der Dampfkiste lassen sich die Holzfasern durch Druck klaglos ineinander schieben (verkürzen). Dagegen lassen sie sich schlecht auseinander ziehen, bereits eine leichte Dehnung führt zum Bruch. Das ist der Fall bei dickeren Leisten oder engeren Radien.3. Die Oberfläche des Rohlings und die Biegefläche der Form müssen glatt sein. Dadurch wird das Ineinanderschieben der Fasern an der innenseite der Biegung nicht "gebremst". Die Biegefläche der Form belege ich daher mit einem Streifen aus Niroblech.
4. Es muss verhindert werden, dass die Fasern an der Außenseite der Biegung länger werden. Dies wird dadurch erreicht, dass der Rohling zwischen zwei Holzklötzen eingeklemmt wird, die an einem Stahlband (Kompressionsband) festgeschraubt sind. Den genauen Abstand dieser Anschlagklötze muss im nassen Zustand des Rohlings eingestellt werden. Seine Länge ändert sich nicht mehr nach dem Dämpfen. Beim Biegen können sich die äußeren Schichten nicht verlängern, nur die Innenseite wird dann kürzer.
5. Da es beim Biegen alles schnell gehen muss, ist es vorteilhaft, wenn man vorher die Bewegungsabläufe eingeübt hat.
6. Das Hantieren mit Schraubzwingen nimmt viel Zeit in Anspruch. Durchgesteckte Bolzen und Keile sind schneller und sicherer.
7. Das Holz erst in die Kiste legen, wenn die angezeigte Temperatur ca. 95 °C überschritten hat. Ab dann, keine Unterbrechung, sonnst muss man wieder von vorn anfangen.
8. Nach der Dämpfzeit (ca. 1 Stunden pro Zoll) wird der Rohling eingeklemmt und zügig um die Form gebogen. Streckenweise werden die Haltebolzen durchgesteckt und mit Keilen gesichert.

Vorbereitete Biegeform. Auf der Innenfläche, das "Rutschband". Auf der rechten Seite, das Kompressionsband, einseitig befestigt und bereits auf die Länge der Leiste eingestellt

Die 1-Zoll-Mahagonileiste nach dem Biegen. Außen, das Kompressionsband mit den Anschlagklötzen (Reststücke Mahagonileiste)
Nach ein paar Stunden können die Metallbänder entfernt werden. Die Leiste muss jedoch fest geklemmt auf der Form bleiben, damit sie vollständig trocknen kann (ca. 1 Woche).